Как сделать вагон – Как делают вагоны для РЖД: russos — LiveJournal
Как делают вагоны для РЖД
Каждый раз, попадая на интересное и масштабное производство, я готов там находиться сутками, снимая интересные кадры, вникая в тонкости производства и технологий. Это безумно увлекательно. Сегодня побываем на самом крупном предприятии России и СНГ и посмотрим, как делают вагоны для поезда.
1. Я приехал на Тверской вагоностроительный завод около 10 утра, и первоначально планировал закончить как раз к презентации новой электрички. Но куда там! К двум часам мы только-только отсняли цеха, где производятся комплектующие… а после презентации наконец-то приступили к самому главному — сборочным цехам. Мои сопровождающие явно планировали освободиться с работы вовремя — в 17:00, но, простите, уйти рано оттуда просто невозможно. В итоге съемка завершилась в половине седьмого, да и то осталось еще масса моментов, которые можно было бы посмотреть.
А потом — другая проблема. На производстве я отснял более 1 000 кадров. Брак, повторы и неудачные ракурсы выкидывались сразу. Между прочим, это 800 с чем-то кадров в корзину получилось. И место сэкономилось. Ещё сотня выкинется после повторного прохода. И дальше начинается кропотливая работа: как из оставшихся 300 выбрать те, что нужны для поста. Это ад, друзья, на самом деле. Дело в том, что отснято очень сложное и многоплановое производство, и хочется показать всё. Некоторые кадры нужны для понимания технических процессов, а некоторые просто красивые.
Итак, после небольшого вступления — Тверской вагоностроительный завод. Самое крупное предприятие России и СНГ по производству различных типов пассажирских вагонов и комплектующих к ним. Основной поставщик вагонов для ОАО «РЖД».
Имеющиеся производственные площади и технологические мощности позволяют одновременно вести работы по изготовлению нескольких моделей пассажирских вагонов, а также различных типов грузовых вагонов и вагонов специального назначения.
Завод был основан в 1898 году французско-бельгийским акционерным обществом «Диль и Бакалан» под названием «Верхневолжский завод железнодорожных материалов». В 1915 году его переименовали в Тверской Русско-Балтийский вагонный завод, а после национализации (в 1918 году) — Тверской вагоностроительный завод.
02. С первых лет ХХ века на заводе началась эпоха пассажирского вагоностроения. На архивной фотографии двухэтажный вагон, созданный на ТВЗ в 1905 году:
03. У завода огромная площадь в Твери, да и по сути это единственное крупное работающее предприятие в этом городе. На территории можно увидеть постройки различных эпох и видов. Например, на фотографии вы видите самую старую постройку — деревянный сруб водонапорной башни местной котельной. Стоит он аж с XIX века:
04. Но свою экскурсию мы начинаем с деревообрабатывающего цеха. Сейчас, в современном вагоне дерева используется очень мало, а раньше почти весь вагон был деревянным. Этот станок делает детали любой конфигурации обрабатывает за считанные минуты, точность высочайшая, что сказывается соответственно на точности и скорости сборки готовых вагонов.
05. Рабочий приклеивает суперклеем на купейные двери резиновые уплотнители. Около половины 12-го утра, а он уже столько тюбиков клея израсходовал:
06. На станке пилят одновременно четыре металлических профиля, которые в дальнейшем станут частью внутреннего оборудования вагона:
07. А теперь пройдем и посмотрим, как делают металлические детали будущего вагона. Это лист металла после плазменной резки:
08. Штамповочные станки. Часть мелкой фурнитуры и деталей, когда их применяемое количество велико, не выгодно делать с помощью новых технологий (дорого и менее производительно), поэтому используют такой станочный парк. А рядом стоит старый пресс очень лохматых годов. Но в абсолютно работоспособном состоянии.
09. Окраска деталей осуществляется порошковыми красками на автоматической линии.
10. Теперь пора сделать рамы для подвагонных тележек. В дело вступает автоматический робот-сварщик. Труднодоступные места провариваются вручную:
11. Почти законченная рама тележки:
12. Производство колесных пар:
13. Насадка колеса на ось. Существует горячий и холодный метод насадки. Здесь применяется холодный. Внутренний диаметр отверстия в колесе чуть-чуть меньше наружного диаметра оси. И колесо прессом насаживается на ось:
14. Готовые колёсные пары отправляются на сборку тележек:
15. Готовая тележка новой конструкции пассажирского вагона с дисковыми тормозами:
16. А теперь пройдем в литейный цех. На этом невзрачном фото вы видите буквально технический переворот в литейном деле. Если вам надо отлить простую деталь без полостей внутри, то это все просто. А вот если деталь сложная и внутри находятся полости и каналы? Внутренние полости формируются с помощью песчаных моделей. Раньше их трамбовали вручную, сейчас песчаные модели делает машина. Результат ее работы — на фото:
17. Выдача чугуна:
18. Успевают залить несколько опок и снова идут на выдачу чугуна:
19. Теперь идем смотреть на сборку кузовов. Сначала сваривают раму вагона, затем устанавливают подвагонное оборудование и прокладывают коммуникации.
20. Параллельно со сборкой рам кузовов на специальной линии изготавливаются боковины вагонов:
21. Обшивка крыши сначала сваривается в плоском виде, потом переворачивается и на специальном стенде ей придается полукруглая форма:
22. Наконец-то все части кузова (рама, боковины, торцевые стены и крыша) соединяются вместе в готовое изделие — основу будущего вагона:
23. Вагон почти готов. По крайней мере его каркас:
24. Вагон после нанесения теплоизоляционного покрытия и настила пола.
25. Далее идет по сути обычная сборка огромного количества комплектующих и их проверка. Сборка производится на позициях — на каждой выполняются только определенные действия. Потом вагон передвигается на следующую позицию. Сюда они приходят уже покрашенными:
26. Вагон после установки почти всех внутренних систем. Теперь пора устанавливать перегородки и монтировать то, что в итого будет видеть пассажир.
27.
28. Новые вагоны с местами для сидения теперь включают и в поезда постоянного формирования, в том числе и фирменные.
29. Полный цикл производства вагона занимает около 70 дней. Для двухэтажного вагона эта цифра составляет около 100 дней. Это период от изготовления первой детали до готового вагона.
30. А это подъемник для инвалидов штабном вагоне:
31. Двухэтажный вагон разработанный по инициативе РЖД:
32. Спальные вагоны габарита RIC для международных сообщений:
33. В каждом купейном вагоне есть душ.
34. И умывальник под столиком. А вот открывашки под ним нет.
За кадром остались покрасочные цеха, климатическая станция для испытаний, центральная заводская лаборатория и много что еще. А до 2030 года РЖД закупит 16.5 тыс. вагонов.
©
ribalych.ru
Как делают вагоны — Русский блоггер
С чем у вас ассоциируется метро? Со станциями, турникетами или с вагонами?
Сегодня я расскажу про то, как создаются железные подземные, и не только, поезда на Метровагонмаше.
1.
2. Мытищинский машиностроительный завод был основан в 1897 в городе Мытищи Московской области. Его основателями стали потомственный почетный гражданин Савва Мамонтов, дворянин Константин Арцыбушев и гражданин Северо-Американских Соединённых штатов, временный Московской 1-й гильдии купец, инженер Александр Бари, которые в декабре 1895 представили в Министерство финансов России проект «Московского акционерного общества вагоностроительного завода». 2 января 1896 Комитет министров разрешил «учреждение означенной Компании», а ее Устав был утвержден Николаем II.
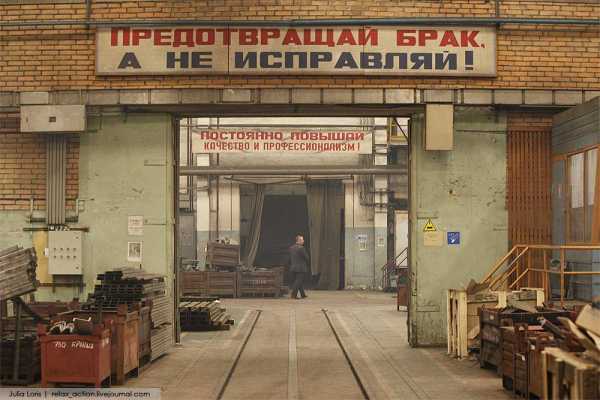
3. По своему техническому оборудованию завод предназначался для постройки подвижного железнодорожного состава и изготовления запасных частей. Первой продукцией завода стали вагоны для Северной железной дороги России.
4. В 1903 началось производство трамвайных вагонов и снегоочистителей для Москвы. В 1926 году впервые в стране на заводе начался выпуск электровагонов (электричек) для первых электрифицированных дорог.
5. На данный момент производство т.н. рельсовых автобусов (вагонов с дизельным двигателем) одна из сохранившихся задач предприятия. Это и штабные вагоны и дизель поезда для не электорофицированных регионов Россиии и других стран, например Сербии.
6. Один из начальных этапов производства рельсовых автобусов — сварочный цех
7.
8. После этого сборка проходит в соседнем цехе. Как раз сербский двойной дизель поезд.
9.
10 Ну, а теперь о большей деятельности Метровагонмаша — это ремонт и изготовление новых вагонов для метрополитена.
11. Как и с автобусными вагонами — здесь все начинается в сварочном цехе. где формируется каркас и общий вид будущего вагона.
12.
13 Человеческий фактор иногда важнее электроники.
14. Многие компании все электрофицируют забывая о том, что человеческий фактор, зачастую,более надежен.
15. В настоящее время Метровагонмаш выпускает вагоны таких типов 81-714.5/717.5, 81-740/741 и 81-760/761.
16. Вагоны серии 740/741 проектировались для Бутовской линии легкого метро, поэтому они ориентированы для работы на открытом воздухе, они как и автобусы имеют гибкое сочленение.
17.
18. В этом же цехе стоят уже готовые тележки.
19.
20. А вот после сборки начинается самое интересное, и первое — это покраска.
21. Здесь вагоны красят, наносят нужные метки, размечают-прикрепляют порядковый номер.
22.
23. Здесь же в цехе вагону делают «мордочку».
24. Время производства одного вагона с «нуля» составляет примерно 70 часов.
25 И вот после предварительного облагораживания наш вагон попадает в руки мастеров, которые наводят окончательный лоск от проводки до отладки.
26.
27 Для меня самым приятным оказалось то, кто занимается монтировкой оборудованием и приведением вагонов в рабочее состояние. Это прекрасные, добрые люди.
28.
29. А теперь просто посмотрите на процесс.
30.
31. Этого вы никогда не увидите, т.к. это скрыто гармошкой).
32. Спасибо вам — это искренне.
33. Кто работает на Метровагонмаше.
34.
35.
36.
37.
38.
39.
40.
41.
42. Раньше Метровагонмаш имел практически полный цикл производства, но усложнение продукции и условия рынка заставили передать часть производств специализированным заводам. Сократились литьевое и кузнечное производства, уменьшился объем работ в термическом цехе.
43.
Автор: Юлия Лорис (оригинал)
Рубрика: Репортаж. Метки: метро, завод, промышленность, Мытищи, производство.Другие публикации
03.11.2018 в 21:25Театр в подземке
В Московском метрополитене запустили поезд к 120-летию МХТ им.Чехова.
Fast. First. FEST!
В конце августа мне довелось попасть с очередным пресс-туром в интересный город Кострому, что на Волге. А поводом для поездки стал визит на предприятие ФЭСТ.
rblogger.ru
как его сделать своими руками
Бывают ситуации, когда человек нуждается во временном жилье, где можно отдохнуть от работы и провести свободное время. Особенно актуальными являются вагоны, которые используют в качестве бытовки, где проживают строители, охранники и военные. Также вагон может стать неплохим проектом дачного домика и использоваться в личных целях.
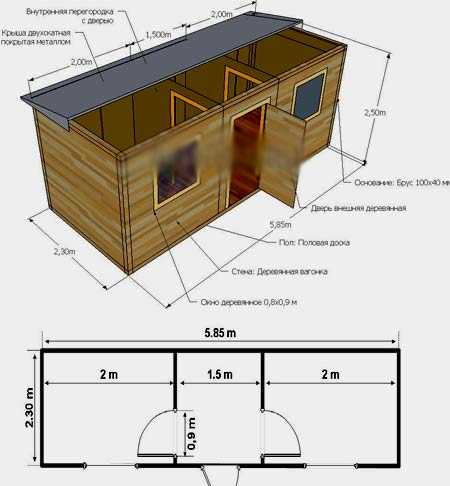
Любое строительство предполагает наличие таких элементов, как схема и чертеж. Именно графическое изображение позволяет избежать проблем при возведении бытовки. Проект по своей сути несложный, поэтому его вполне можно составить самостоятельно.
Для этого необязательно быть специалистом в черчении, достаточно знать основные конструктивные особенности вагона и суметь изобразить их на бумаге, выполнив разметку. Как сделать полноценный проект и составить чертеж правильно, разберем далее.
Вернуться к оглавлениюСодержание материала
Из каких элементов состоит вагон
На этапе планирования решается вопрос о функциональности бытовки. Именно от этого параметра зависит чертеж и общая схема. Если площадь предполагает временное жилье, сюда обязательно включают три отдельные комнаты:
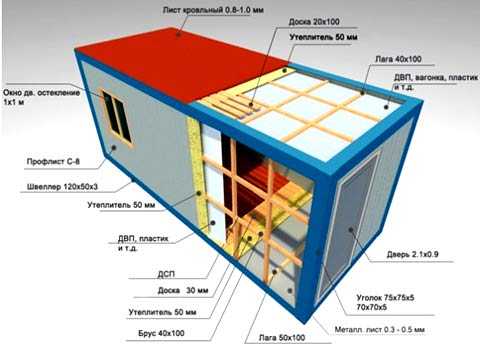
- санузел;
- спальню;
- кухню.
При желании все три комнаты могут быть объединены в одну, и разделяться обычными межкомнатными ширмами. Также обращают внимание на мобильность сооружения. Если есть нужда его перемещения и постановки на колеса, то в проект добавляют еще один чертеж: разметка днища и его крепление к стенам. К отдельным элементам относят окна и двери, а также систему вентиляции, без которой сложно обойтись в столь замкнутом пространстве.
Сам по себе вагон может быть как маленьким, так и большим, предоставляя жилье максимум 5–8 людям одновременно. При присоединении колес бытовка может стать великолепным домом на колесах, благодаря которому можно путешествовать по миру вместе со своим жилищем.
Вернуться к оглавлениюКак сделать чертеж
Перед началом работы линейкой производят соответствующие замеры. Высота сооружения должна быть не менее роста человека плюс 50 см. Это создаст наиболее комфортные условия для проживания, сократив траты на дополнительные строительные материалы. Ширину дачного вагончика рассчитывают в соответствии с его назначением, также как и длину. Сюда входят такие показатели:
- Количество проживающих людей;
- Количество комнат;
- Площадь отдельных участков и общая площадь строения;
- Необходимость частой транспортировки вагона на дальние расстояния.
Когда все замеры произведены, приступают к начертанию. Заметим, что чертежи можно создать не только своими руками при помощи бумаги и карандаша, но и с помощью специальных графических редакторов. Последние значительно экономят время и позволяют производить дополнительные расчеты количества нужного строительного материала.
Чертеж и планировка с размерами строительного вагончикаЕсли нет возможности подключить компьютерные технологии, когда создается проект бытовки, можно сделать чертеж. Основной чертеж (вид сверху) должен отображать следующие показатели:
- Стены и их толщину;
- Расположение комнат;
- Средства коммуникаций и их расположение.
Если комнат много, требуются дополнительные чертежи отдельных комнат, где более детально изображают все компоненты, вплоть до расположения мебели. Если есть возможность создания двухмерного изображения, то можно сделать чертеж своими руками наружной части вагончика, где указывается каркас, его толщина и место крепления. Такая схема более чем удовлетворительна для возведения самого примитивного вагончика, используемого в качестве бытовки.
Вернуться к оглавлениюДля чего нужен чертеж
Чертежи являются не только ориентиром при строительстве своими руками.
Они представляют собой полноценный документ, который утверждается застройщиком (при использовании в коммерческих целях). Если бытовки возводятся для домашнего пользования, их каркас может иметь различную жесткость. Для строительного проекта чертеж должен учитывать все тонкости, а также строительный материал, используемый при возведении сооружения.
Схематическое изображение наглядно показывает проектируемый объект, позволяя исключить вариант неудобств и просчетов еще на этапе планирования, экономя время на дальнейшие переделки.
Также чертежи помогают экономить. Как бы странно это ни звучало, но возвести каркас бытовки и обшить его листами металла гораздо дешевле, нежели купить уже готовый вагончик. К любому чертежу прилагается ТО (техническое обоснование), где более подробно словами описывается проектируемый вагончик.
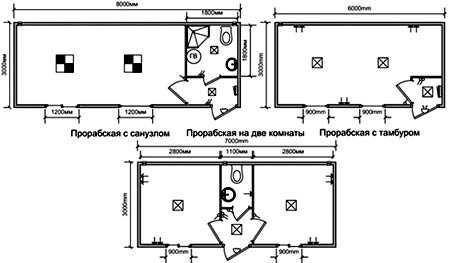
Благодаря этому можно учесть все детали и произвести предварительный подсчет стоимости работ. Чертеж позволяет быстро и правильно собрать каркас и стены своими руками, превратив вагончик в жилую площадь. Такие бытовки, где каркас имеет дополнительные ребра жесткости можно использовать в качестве полноценных домов, дополнительно утеплив стены.
Вернуться к оглавлениюЕсли чертеж не удался
Если чертить самостоятельно вы не сумели, не беда. Всегда можно решить проблему как минимум двумя способами.
Вариант 1. Заказать чертеж у профессионалов. Можно обратиться в любую строительную компанию, предоставляющую услуги по проектированию и заказать нужный чертеж, который будет готов в считаные часы и с учетом личных пожеланий. В таком случае каркас, обшивка и другие комплектующие указываются, вплоть до модели и формы, в приложениях, прикрепленных к основному чертежу.
Вариант 2. Купить готовый вагон. Если своими руками, вообще, проблематично что-либо сделать (не только чертеж), то лучше не тратить время, силы и деньги, а сразу купить готовый вагончик-бытовку.
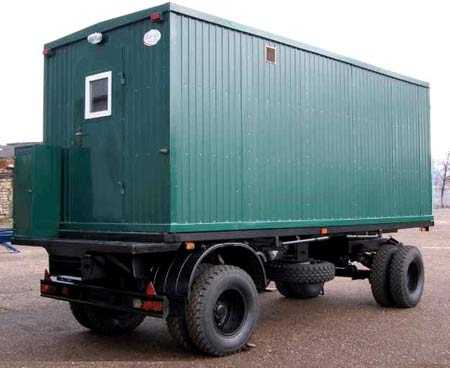
Как видим, чертеж — это важная и неотъемлемая часть стройки, роль которой сложно переоценить. Он помогает предварительно оценить будущее строение, выявить его плюсы и минусы, а также внести коррективы на бумаге, чтобы не столкнуться с проблемами при возведении металлической бытовки своими руками. Если при его создании возникают проблемы, всегда можно обратиться за помощью к специалистам, выполняющим подобные работы ежедневно.
proekt-sam.ru
Вагоны из картона
«Народным очумельцам посвящается»
Если ваши желания в построении макета железной дороги превосходят возможности серийного производства, самое время задуматься над тем, чтобы самому сделать себе модели. Существуют разные материалы и технологии, — тут рассматривается изготовление из картона.
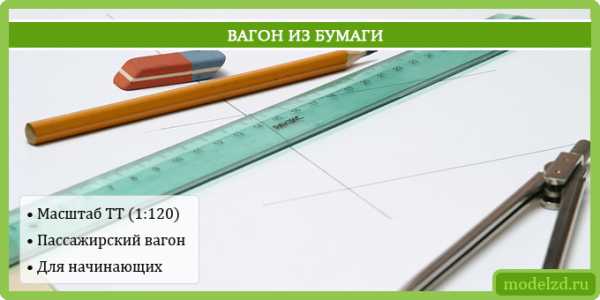
Прежде всего следует запастись всем необходимым.
Для начала нужен хороший белый картон (желательно 0,35 – 0,5 мм – определяется на глаз по линейке).
Также нужны подходящие инструменты:
- механический карандаш со стержнем на 0,5 мм,
- клей ПВА,
- линейка на 30 см,
- уголок,
- стирательная резинка,
- нитки (желательно не очень ворсистые),
- прозрачный пластик, двусторонний скотч,
- наждак двух видов (крупный и мелкий),
- нож для бумаги, ножницы обычные,
- ножницы маникюрные,
- прищепки (желательно пластмассовые с плоскими поверхностями),
- а также еще кое-что по мелочи, о чем будет указано далее.
И главное – нужно искреннее желание сделать макет!
Тут будет рассматриваться производство модели на уже готовой ходовой части. В качестве донора можно использовать вагоны от ТТ-модель или ВТТВ.
При производстве какого-либо макета необходимы справочные материалы в виде чертежей и иллюстраций объекта моделирования. Для экономии времени я также использовал ЦМВ от ТТ-модель.
Итак, начнем. Если используется чертеж, то все размеры нужно пересчитать в соответствующем масштабе, в моем случае – 1:120. Далее на листе картона следует нарисовать базовую развертку вагона БЕЗ крыши (в результате должен получиться вытянутый параллелепипед без пола) (Рис. 1).
Теперь необходимо повысить жесткость будущего кузова – с обратной стороны нужно наклеить на стенки второй слой картона с уже прорезанными окнами так, чтобы окна между собой совпали (Рис. 2).
Так как картон при намокании имеет нехорошее свойство разбухать, то много мазать клея не надо, а надо быстро и тонким слоем намазать одну сторону и сразу крепко прижать и положить под пресс.
Теперь займемся ребрами жесткости. Делаются они из ниток, которые наклеиваются вдоль нарисованных линий: сначала наносится клеевая полоска, на которую потом накладывается нитка и прижимается пальцем. Суть в том, чтобы пропитать нитку клеем и убрать лишний клей с поверхности. Когда все ребра наклеены, пора очертить двери. Для этого по контуру двери вырезает тонкую канавку ножом. После этого промазываем вырезанные контуры дверей и уже наклеенные нитки. Когда все подсохло, по поверхности ниток надо аккуратно пройтись мелким наждаком и еще раз промазать клеем. При всех промазываниях стараемся оставлять как можно меньше клея, чтобы потом не повылезали лишние неровности. Поручни делаются из тонких полосок картона.
Теперь пора заняться сборкой. Места сгибов с обратной стороны продавливаем ножницами. Потом вырезаем, тщательно сгибаем и склеиваем (Рис. 3).
Крыша.Чтобы получить крышу нужной формы, сначала требуется создать параллелепипед из наслоенного картона, высота которого равняется высоте самой крыши (обычно красится в серый цвет). Ширина и длина должны на 1 и 2 мм превышать ширину и длину заготовки вагона соответственно (это примерные показатели). Это необходимо для того, чтобы после склейки крыши (кстати, тоже желательно клеить при помощи пресса) можно было зашлифовать с боков и тем самым подогнать под размер вагона. Далее крыше нужно придать выпуклую форму – для этого с торцов рисуем профиль крыши и продольно срезаем лишнее. После этого шлифуем сначала крупным наждаком, а потом и мелким. После этого обмазываем крышу клеем и ждем пока высохнет. Обрабатываем мелким наждаком и повторяем операцию. Теперь можно приклеивать крышу. Если найдете, чем прижать ее пока будет сохнуть, будет хорошо. Если в оригинале на крыше есть ребра жесткости, то они делаются аналогичным образом при помощи ниток. Стык крыши с кузовом промазываем клеем. После этого на крышу можно прикрепить воздухозаборники. С торцов вагона наклеиваем картон, чтобы скрыть стык, хотя, в зависимости от ситуации, можно обойтись без этого. При помощи зубочисток делаются переходные суфле (Рис. 4).
Поговорим немного о внутренностях. Для начала нужно сделать пол из 2-3х слоев картона. Далее на нем размечаем схему перегородок, которые после вырезания «ставим» на клей. Общая высота внутренностей с полом должна подбираться с учетом высоты ходовой части. К стенкам клеим верхние полки, а нижние, скорее всего, придется клеить на пол. После этого поверх перегородок клеится полоска картона шириной 1 см и длиной на 2 см меньше длины вагона.
Теперь можно красить. Желательно использовать несмываемые водой краски. Можно использовать аэрозольные, обычные масляные или специальные модельные краски. Дальше используем скотч и кисточки разных размеров для получения желаемой окраски.
Когда все высохло, со внутренней стороны стенок вагона при помощи двустороннего скотча наклеиваем полоски прозрачного пластика. Со внутренней же стороны на крышу наклеиваем двусторонний скотч, а потом к нему прижимаем внутренности вагона. Снизу на пол вагона опять клеим двусторонний скотч и прижимает к нему ходовую часть (Рис. 5).
Вагон готов!
Смотите также видео, как сделать грузовой вагон из картона:
Читайте также:
www.modelzd.ru
Как собирают железнодорожные вагоны | Наука и жизнь
Каждый раз, попадая на интересное и масштабное производство, я готов там находиться сутками, снимая интересные кадры, вникая в тонкости производства и технологий. Это безумно увлекательно. Сегодня побываем на самом крупном предприятии России и СНГ и посмотрим, как делают вагоны для поезда.
Фотографии и текст Александра Попова
1. Я приехал на Тверской вагоностроительный завод около 10 утра, и первоначально планировал закончить как раз к презентации новой электрички. Но куда там! К двум часам мы только-только отсняли цеха, где производятся комплектующие… а после презентации наконец-то приступили к самому главному — сборочным цехам. Мои сопровождающие явно планировали освободиться с работы вовремя — в 17:00, но, простите, уйти рано оттуда просто невозможно. В итоге съемка завершилась в половине седьмого, да и то осталось еще масса моментов, которые можно было бы посмотреть.
А потом — другая проблема. На производстве я отснял более 1 000 кадров. Брак, повторы и неудачные ракурсы выкидывались сразу. Между прочим, это 800 с чем-то кадров в корзину получилось. И место сэкономилось. Ещё сотня выкинется после повторного прохода. И дальше начинается кропотливая работа: как из оставшихся 300 выбрать те, что нужны для поста. Это ад, друзья, на самом деле. Дело в том, что отснято очень сложное и многоплановое производство, и хочется показать всё. Некоторые кадры нужны для понимания технических процессов, а некоторые просто красивые.
Итак, после небольшого вступления — Тверской вагоностроительный завод. Самое крупное предприятие России и СНГ по производству различных типов пассажирских вагонов и комплектующих к ним. Основной поставщик вагонов для ОАО «РЖД».
Имеющиеся производственные площади и технологические мощности позволяют одновременно вести работы по изготовлению нескольких моделей пассажирских вагонов, а также различных типов грузовых вагонов и вагонов специального назначения.
Завод был основан в 1898 году французско-бельгийским акционерным обществом «Диль и Бакалан» под названием «Верхневолжский завод железнодорожных материалов». В 1915 году его переименовали в Тверской Русско-Балтийский вагонный завод, а после национализации (в 1918 году) — Тверской вагоностроительный завод.
02. С первых лет ХХ века на заводе началась эпоха пассажирского вагоностроения. На архивной фотографии двухэтажный вагон, созданный на ТВЗ в 1905 году:
03. У завода огромная площадь в Твери, да и по сути это единственное крупное работающее предприятие в этом городе. На территории можно увидеть постройки различных эпох и видов. Например, на фотографии вы видите самую старую постройку — деревянный сруб водонапорной башни местной котельной. Стоит он аж с XIX века:
04. Но свою экскурсию мы начинаем с деревообрабатывающего цеха. Сейчас, в современном вагоне дерева используется очень мало, а раньше почти весь вагон был деревянным. Этот станок делает детали любой конфигурации обрабатывает за считанные минуты, точность высочайшая, что сказывается соответственно на точности и скорости сборки готовых вагонов.
05. Рабочий приклеивает суперклеем на купейные двери резиновые уплотнители. Около половины 12-го утра, а он уже столько тюбиков клея израсходовал:
06. На станке пилят одновременно четыре металлических профиля, которые в дальнейшем станут частью внутреннего оборудования вагона:
07. А теперь пройдем и посмотрим, как делают металлические детали будущего вагона. Это лист металла после плазменной резки:
08. Штамповочные станки. Часть мелкой фурнитуры и деталей, когда их применяемое количество велико, не выгодно делать с помощью новых технологий (дорого и менее производительно), поэтому используют такой станочный парк. А рядом стоит старый пресс очень лохматых годов. Но в абсолютно работоспособном состоянии.
09. Окраска деталей осуществляется порошковыми красками на автоматической линии.
10. Теперь пора сделать рамы для подвагонных тележек. В дело вступает автоматический робот-сварщик. Труднодоступные места провариваются вручную:
11. Почти законченная рама тележки:
12. Производство колесных пар:
13. Насадка колеса на ось. Существует горячий и холодный метод насадки. Здесь применяется холодный. Внутренний диаметр отверстия в колесе чуть-чуть меньше наружного диаметра оси. И колесо прессом насаживается на ось:
14. Готовые колёсные пары отправляются на сборку тележек:
15. Готовая тележка новой конструкции пассажирского вагона с дисковыми тормозами:
16. А теперь пройдем в литейный цех. На этом невзрачном фото вы видите буквально технический переворот в литейном деле. Если вам надо отлить простую деталь без полостей внутри, то это все просто. А вот если деталь сложная и внутри находятся полости и каналы? Внутренние полости формируются с помощью песчаных моделей. Раньше их трамбовали вручную, сейчас песчаные модели делает машина. Результат ее работы — на фото:
17. Выдача чугуна:
18. Успевают залить несколько опок и снова идут на выдачу чугуна:
19. Теперь идем смотреть на сборку кузовов. Сначала сваривают раму вагона, затем устанавливают подвагонное оборудование и прокладывают коммуникации.
20. Параллельно со сборкой рам кузовов на специальной линии изготавливаются боковины вагонов:
21. Обшивка крыши сначала сваривается в плоском виде, потом переворачивается и на специальном стенде ей придается полукруглая форма:
22. Наконец-то все части кузова (рама, боковины, торцевые стены и крыша) соединяются вместе в готовое изделие — основу будущего вагона:
23. Вагон почти готов. По крайней мере его каркас:
24. Вагон после нанесения теплоизоляционного покрытия и настила пола. Кликабельно, 2312×900 px:
25. Далее идет по сути обычная сборка огромного количества комплектующих и их проверка. Сборка производится на позициях — на каждой выполняются только определенные действия. Потом вагон передвигается на следующую позицию. Сюда они приходят уже покрашенными:
26. Вагон после установки почти всех внутренних систем. Теперь пора устанавливать перегородки и монтировать то, что в итого будет видеть пассажир. Кликабельно, 2510×900 px:
27. Кликабельно, 3553×900 px:
28. Новые вагоны с местами для сидения теперь включают и в поезда постоянного формирования, в том числе и фирменные.
29. Полный цикл производства вагона занимает около 70 дней. Для двухэтажного вагона эта цифра составляет около 100 дней. Это период от изготовления первой детали до готового вагона.
30. А это подъемник для инвалидов штабном вагоне:
31. Двухэтажный вагон разработанный по инициативе РЖД:
32. Спальные вагоны габарита RIC для международных сообщений:
33. В каждом купейном вагоне есть душ.
34. И умывальник под столиком. А вот открывашки под ним нет.
За кадром остались покрасочные цеха, климатическая станция для испытаний, центральная заводская лаборатория и много что еще. А до 2030 года РЖД закупит 16.5 тыс. вагонов.
nauka.boltai.com
Как делают вагоны для поезда
Каждый раз, попадая на интересное и масштабное производство, я готов там находиться сутками, снимая интересные кадры, вникая в тонкости производства и технологий. Это безумно увлекательно. Сегодня побываем на самом крупном предприятии России и СНГ и посмотрим, как делают вагоны для поезда.
34 фото
Фотографии и текст Александра Попова
1. Я приехал на Тверской вагоностроительный завод около 10 утра, и первоначально планировал закончить как раз к презентации новой электрички. Но куда там! К двум часам мы только-только отсняли цеха, где производятся комплектующие… а после презентации наконец-то приступили к самому главному — сборочным цехам. Мои сопровождающие явно планировали освободиться с работы вовремя — в 17:00, но, простите, уйти рано оттуда просто невозможно. В итоге съемка завершилась в половине седьмого, да и то осталось еще масса моментов, которые можно было бы посмотреть.
А потом — другая проблема. На производстве я отснял более 1 000 кадров. Брак, повторы и неудачные ракурсы выкидывались сразу. Между прочим, это 800 с чем-то кадров в корзину получилось. И место сэкономилось. Ещё сотня выкинется после повторного прохода. И дальше начинается кропотливая работа: как из оставшихся 300 выбрать те, что нужны для поста. Это ад, друзья, на самом деле. Дело в том, что отснято очень сложное и многоплановое производство, и хочется показать всё. Некоторые кадры нужны для понимания технических процессов, а некоторые просто красивые.
Итак, после небольшого вступления — Тверской вагоностроительный завод. Самое крупное предприятие России и СНГ по производству различных типов пассажирских вагонов и комплектующих к ним. Основной поставщик вагонов для ОАО «РЖД».
Имеющиеся производственные площади и технологические мощности позволяют одновременно вести работы по изготовлению нескольких моделей пассажирских вагонов, а также различных типов грузовых вагонов и вагонов специального назначения.
Завод был основан в 1898 году французско-бельгийским акционерным обществом «Диль и Бакалан» под названием «Верхневолжский завод железнодорожных материалов». В 1915 году его переименовали в Тверской Русско-Балтийский вагонный завод, а после национализации (в 1918 году) — Тверской вагоностроительный завод.
02. С первых лет ХХ века на заводе началась эпоха пассажирского вагоностроения. На архивной фотографии двухэтажный вагон, созданный на ТВЗ в 1905 году:
03. У завода огромная площадь в Твери, да и по сути это единственное крупное работающее предприятие в этом городе. На территории можно увидеть постройки различных эпох и видов. Например, на фотографии вы видите самую старую постройку — деревянный сруб водонапорной башни местной котельной. Стоит он аж с XIX века:
04. Но свою экскурсию мы начинаем с деревообрабатывающего цеха. Сейчас, в современном вагоне дерева используется очень мало, а раньше почти весь вагон был деревянным. Этот станок делает детали любой конфигурации обрабатывает за считанные минуты, точность высочайшая, что сказывается соответственно на точности и скорости сборки готовых вагонов.
05. Рабочий приклеивает суперклеем на купейные двери резиновые уплотнители. Около половины 12-го утра, а он уже столько тюбиков клея израсходовал:
06. На станке пилят одновременно четыре металлических профиля, которые в дальнейшем станут частью внутреннего оборудования вагона:
07. А теперь пройдем и посмотрим, как делают металлические детали будущего вагона. Это лист металла после плазменной резки:
08. Штамповочные станки. Часть мелкой фурнитуры и деталей, когда их применяемое количество велико, не выгодно делать с помощью новых технологий (дорого и менее производительно), поэтому используют такой станочный парк. А рядом стоит старый пресс очень лохматых годов. Но в абсолютно работоспособном состоянии.
09. Окраска деталей осуществляется порошковыми красками на автоматической линии.
10. Теперь пора сделать рамы для подвагонных тележек. В дело вступает автоматический робот-сварщик. Труднодоступные места провариваются вручную:
11. Почти законченная рама тележки:
12. Производство колесных пар:
13. Насадка колеса на ось. Существует горячий и холодный метод насадки. Здесь применяется холодный. Внутренний диаметр отверстия в колесе чуть-чуть меньше наружного диаметра оси. И колесо прессом насаживается на ось:
14. Готовые колёсные пары отправляются на сборку тележек:
15. Готовая тележка новой конструкции пассажирского вагона с дисковыми тормозами:
16. А теперь пройдем в литейный цех. На этом невзрачном фото вы видите буквально технический переворот в литейном деле. Если вам надо отлить простую деталь без полостей внутри, то это все просто. А вот если деталь сложная и внутри находятся полости и каналы? Внутренние полости формируются с помощью песчаных моделей. Раньше их трамбовали вручную, сейчас песчаные модели делает машина. Результат ее работы — на фото:
17. Выдача чугуна:
18. Успевают залить несколько опок и снова идут на выдачу чугуна:
19. Теперь идем смотреть на сборку кузовов. Сначала сваривают раму вагона, затем устанавливают подвагонное оборудование и прокладывают коммуникации.
20. Параллельно со сборкой рам кузовов на специальной линии изготавливаются боковины вагонов:
21. Обшивка крыши сначала сваривается в плоском виде, потом переворачивается и на специальном стенде ей придается полукруглая форма:
22. Наконец-то все части кузова (рама, боковины, торцевые стены и крыша) соединяются вместе в готовое изделие — основу будущего вагона:
23. Вагон почти готов. По крайней мере его каркас:
24. Вагон после нанесения теплоизоляционного покрытия и настила пола. Кликабельно, 2312×900 px:
25. Далее идет по сути обычная сборка огромного количества комплектующих и их проверка. Сборка производится на позициях — на каждой выполняются только определенные действия. Потом вагон передвигается на следующую позицию. Сюда они приходят уже покрашенными:
26. Вагон после установки почти всех внутренних систем. Теперь пора устанавливать перегородки и монтировать то, что в итого будет видеть пассажир. Кликабельно, 2510×900 px:
27. Кликабельно, 3553×900 px:
28. Новые вагоны с местами для сидения теперь включают и в поезда постоянного формирования, в том числе и фирменные.
29. Полный цикл производства вагона занимает около 70 дней. Для двухэтажного вагона эта цифра составляет около 100 дней. Это период от изготовления первой детали до готового вагона.
30. А это подъемник для инвалидов штабном вагоне:
31. Двухэтажный вагон разработанный по инициативе РЖД:
32. Спальные вагоны габарита RIC для международных сообщений:
33. В каждом купейном вагоне есть душ.
34. И умывальник под столиком. А вот открывашки под ним нет.
За кадром остались покрасочные цеха, климатическая станция для испытаний, центральная заводская лаборатория и много что еще. А до 2030 года РЖД закупит 16.5 тыс. вагонов.
Также смотрите «Закат из кабины электропоезда» и «Экспресс Махараджей».
loveopium.ru
Как делают вагоны
Автор:09 июня 2014 14:36
Каждый раз, попадая на интересное и масштабное производство, я готов там находиться сутками, снимая интересные кадры, вникая в тонкости производства и технологий. Это безумно увлекательно.
Так вышло и с Тверским вагоностроительным заводом. К ним я приехал около 10 утра, и первоначально планировал закончить как раз к презентации новой электрички. Но куда там! К двум часам мы только-только отсняли цеха, где производятся комплектующие… а после презентации наконец-то приступили к самому главному — сборочным цехам. Мои сопровождающие явно планировали освободиться с работы вовремя — в 17:00, но, простите, уйти рано оттуда просто невозможно. В итоге съемка завершилась в половине седьмого, да и то осталось еще масса моментов, которые можно было бы посмотреть.
А потом — другая проблема. На производстве я отснял более 1000 кадров. Брак, повторы и неудачные ракурсы выкидывались сразу. Между прочим, это 800 с чем-то кадров в корзину получилось. И место сэкономилось. 🙂 Ещё сотня выкинется после повторного прохода. И дальше начинается кропотливая работа: как из оставшихся 300 выбрать те, что нужны для поста. Это ад, друзья, на самом деле. Дело в том, что отснято очень сложное и многоплановое производство, и хочется показать всё. Некоторые кадры нужны для понимания технических процессов, а некоторые просто красивые. В итоге ужал до 60 штук. Простите, меньше никак не получается.
Итак, после небольшого вступления — Тверской вагоностроительный завод. Самое крупное предприятие России и СНГ по производству различных типов пассажирских вагонов и комплектующих к ним. Основной поставщик вагонов для ОАО «РЖД» (и его «дочки» — ОАО «ФПК»). Предприятие входит в состав «Трансмашхолдинга».
Имеющиеся производственные площади и технологические мощности позволяют одновременно вести работы по изготовлению нескольких моделей пассажирских вагонов, а также различных типов грузовых вагонов и вагонов специального назначения (в один цех снимать не пустили, сказали, что там собирают что-то секретное).
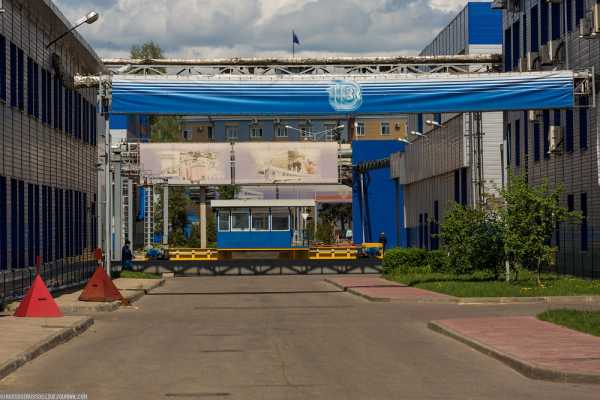
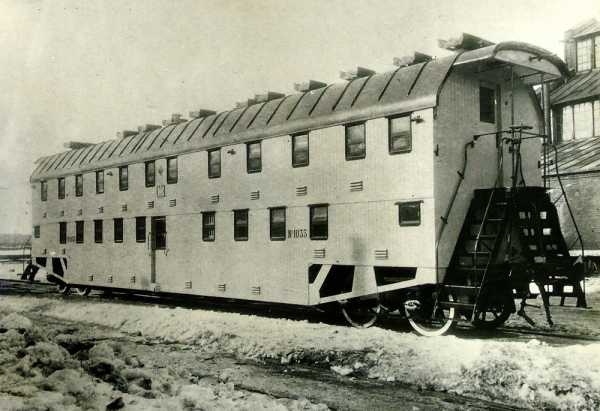
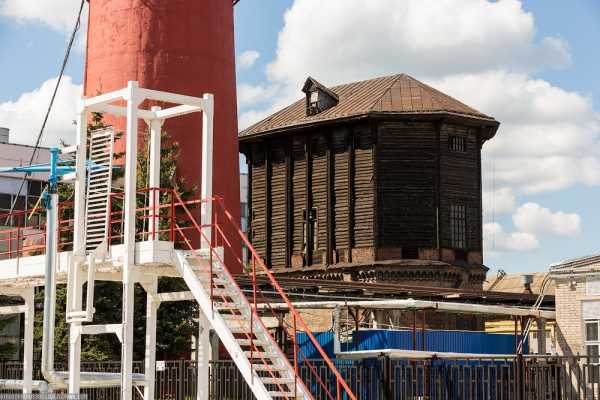
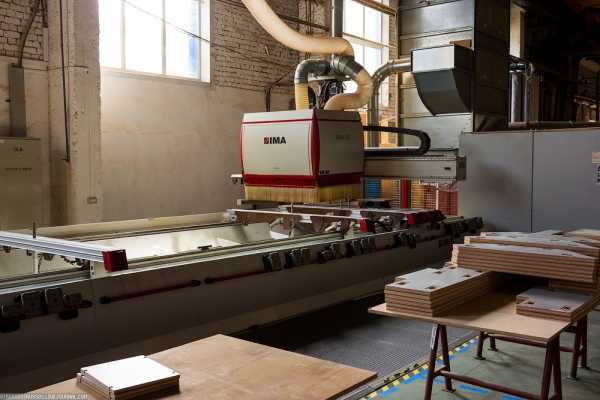
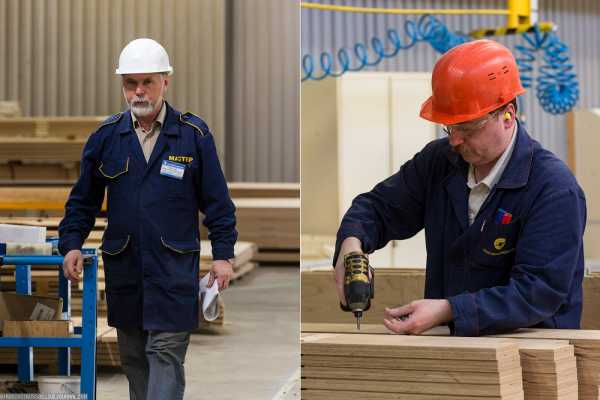
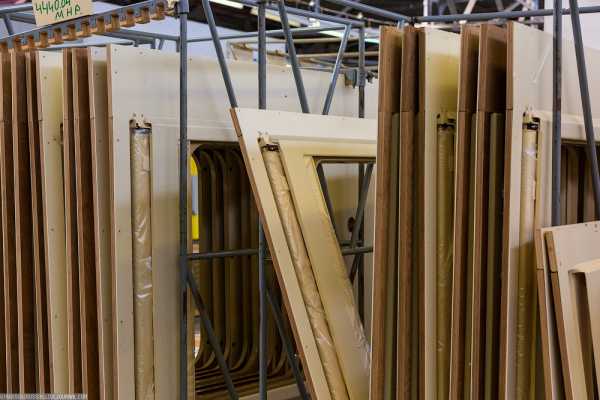
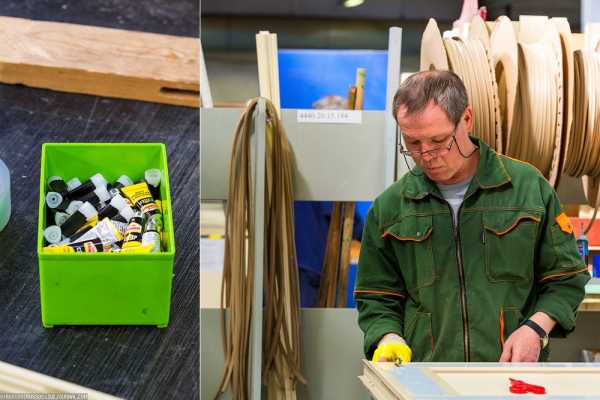
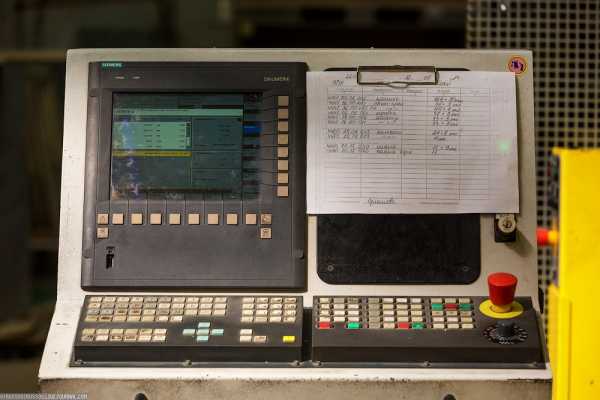
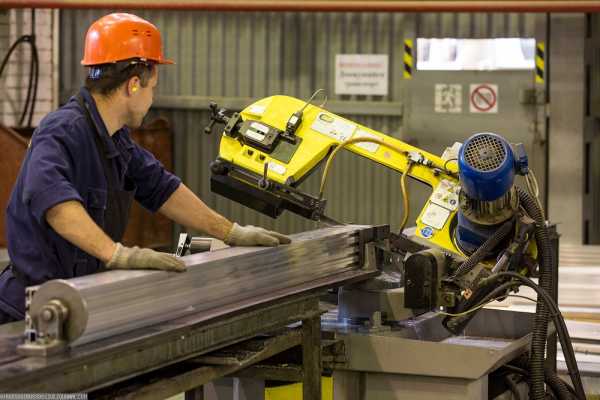
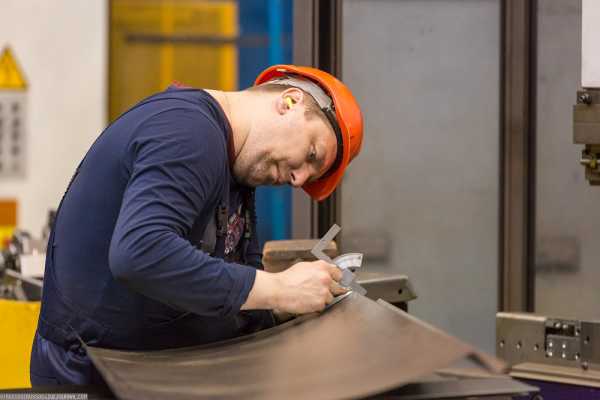
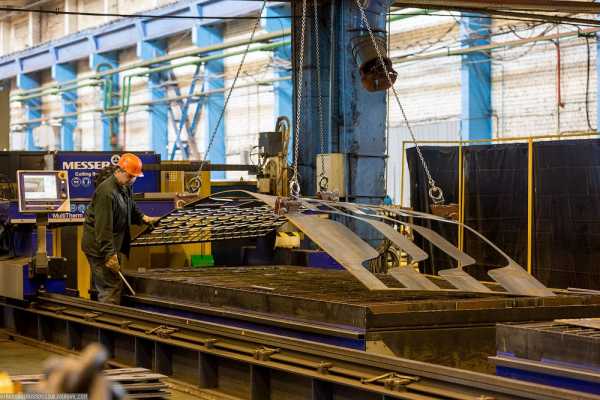
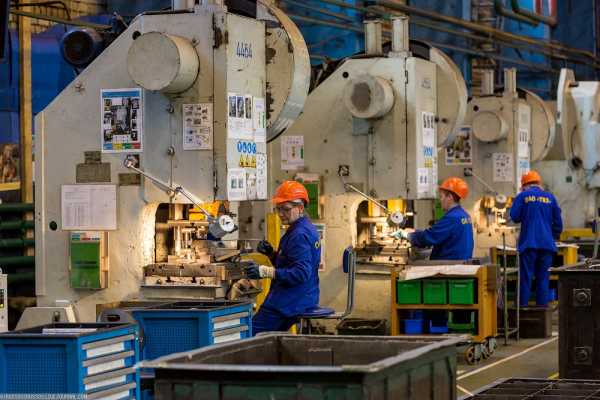
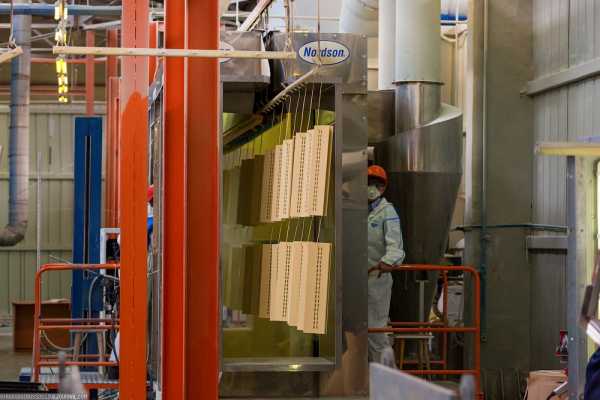
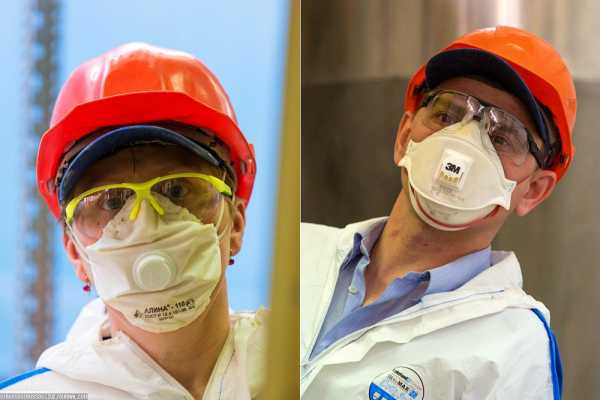
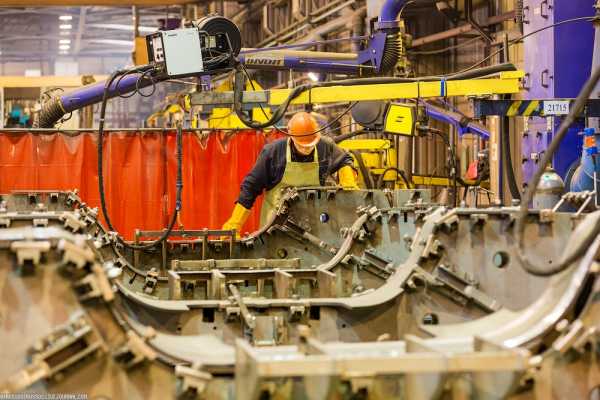

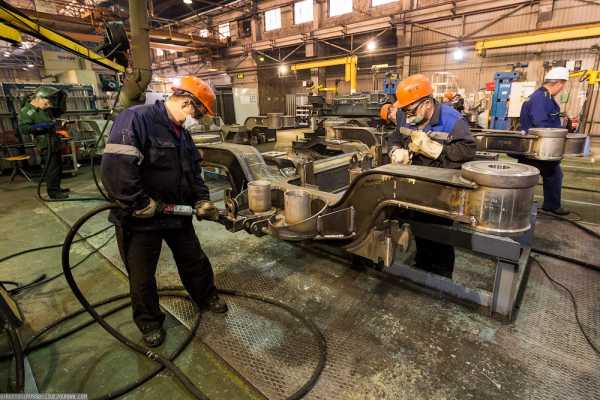
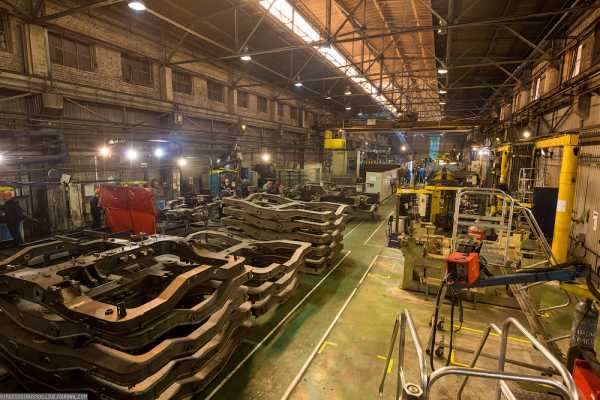
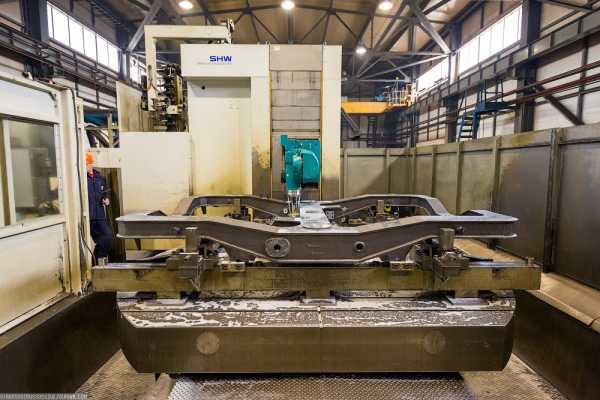
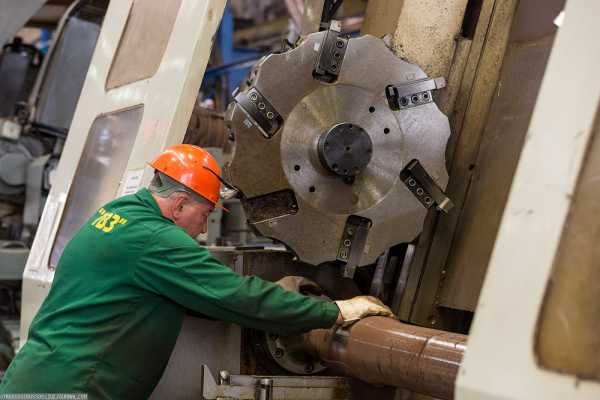
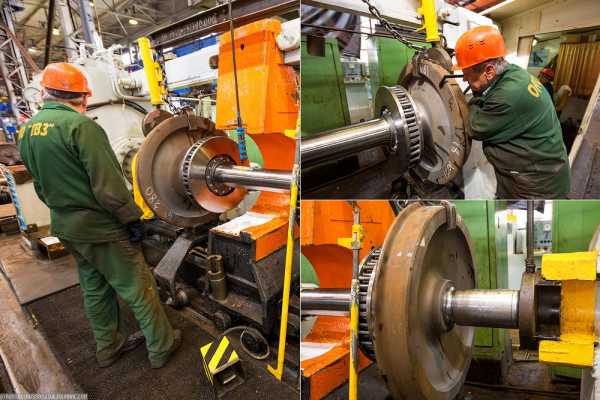
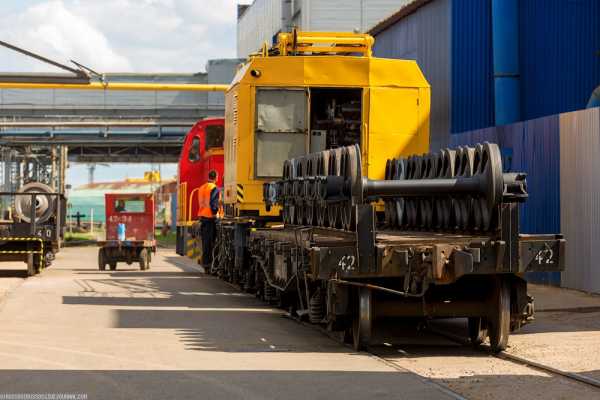
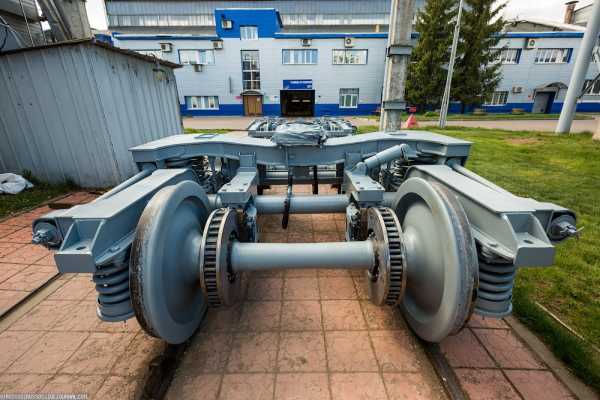
fishki.net
Добавить комментарий